

So I proceed to coat the otherside and smooth out what has seeped through. I have read a couple tutorials that say this is ok and even "You should coat both sides of the screen". I coat the flat underside of the screen with photo emulsion (thin layer with scoop coater) though I can't seem to do it lite enough so the emulsion doesn't go through to the other side. I have watched and read many tutorials on the photo emulsion method but I cannot seem to get it rightġ. I'm new to the photo emulsion method of screen printing and having a bit of trouble. I could also recommend that you go to youtube watch this guy's videos: For example in an ovenĪll words I've mentioned can be imaged by searching for a particular word on google. #12: Cure the ink according to the manufactures specifications. #11: Put it on top of a t-shirt, fill in some ink and use your squeegee to pull the ink across your screen and down onto the t-shirt. #9: Rinse the screen with water and maybe a sponge until all the emulsion which has been located under dark areas of the transparency has been washed out. #8: Turn off the light and take your screen to the bathtub #7: Expose it for around 10 minutes or so. #6: Place the transparency on top of the mesh (mirrored so it will look right when you flip the screen around) and turn on your work lamp suspended over the frame. #5: Flip your now dried (meaning the emulsion is no longer tacky) over so the backside (which will eventually touch the fabric) is upwards. #4: Print something on a transparency (your art) #3: Let the screen (now coated with emulsion) dry for 30min - 2 hours depending on whether you use a fan or not, hot/cold environment, very humid and so on. Not yellow safelight like some people say, just dampen your lights so you can see enough to do the job This should be done in an environment with low intensity light. Start with the back side which will touch the fabric and finish with the inside which will hold the paint. For example one coat on either side or to coats on either side. #2: Fill your scoop coater with emulsion and coat your screen with emulsion. Rinse of all the soap and let the screen dry.
PHOTO EMULSION SCREEN PRINTING FREE
#1: Degrease your screens so they are free from oil, fats and so on. #6: Buy a squeegee for dragging the paint over your screen #4: Buy a 500W halogen work light for exposing your screens. #3: Buy scoop coater for applying the emulsion to the screen () I could recommend Ulano QTX for plasticol ink or Ulano QLT for waterbased. The frames could be fabricated from either alu or wood depending on what tools or friends you have at your service In either case the tubes of the frame should be around 3cm x 3cm - hollow if it's alu and massive if it's wood.ī) Buy the frames and have someone put mesh on them or buy them with mesh on. Elmers glue, wood glue, maybe pieces of paper if you work it right will do the job.A) Fabricate some frames and have someone put mesh on them. I used some white acrylic paint I had on hand. Using the paint I had on hand saved me some money here. Most screen printing uses a photo transfer technique which uses some chemicals, and light and more things to buy specialized. ($7) - The Blocker: This is what you put on the screen, to block the parts you don't want ink to go through. Some kind of latex paint or something similar will probably work too. (Free!) - The Ink: I had some Fabric Screen Printing Ink left over from another shirt project, so I used it.

When it gets stretched a bit it all works out. I used a friends worn out nylon stockings. Anything that the ink you are trying to use will ooze through. ($.75) - The Screen: The most important part. I found a picture frame on clearance for $.75! It is plastic, so washing the ink doesn't do anything real bad to it, and it may hold up longer then cardboard.
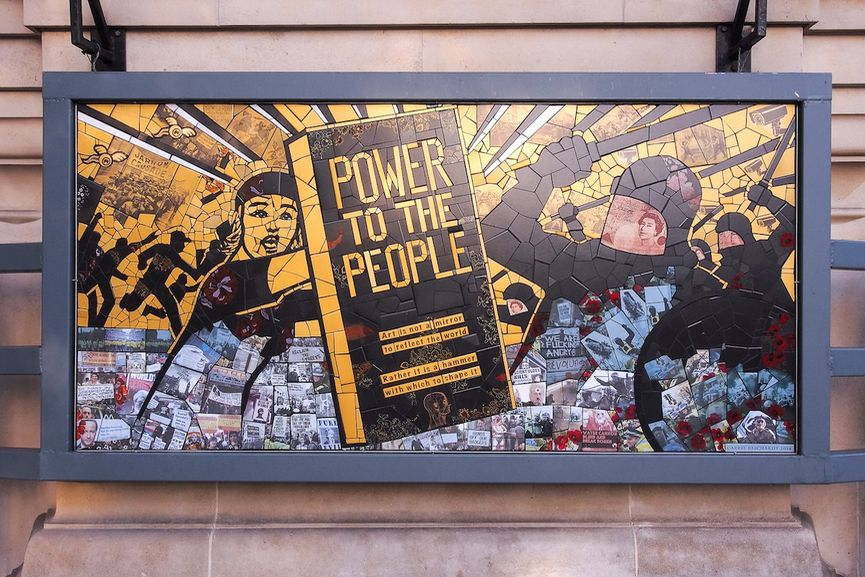
Embroidery hoops, some stiff cardboard, or a bucket with a hole in it. The materials are simple: - Frame: This can really be anything.
